Deodorizing equipment with direct combustion system
The exhaust with odor is combustion with 650 to 850℃ temperature, the odor in exhaust is oxidized and decomposed with high temperature. The exhaust becomes harmless as a result.
The principle and the structure are simple and the system is reliable. However the operation cost for it is high due to the fact that the system uses high temperature.
This deodorizing system is feasible if the client has an exhaust heat recovery equipment and is able to make use of the exhaust.
Advantage:
・The equipment is compact and the initial cost is low
・High deodorizing quality and dependable
・Less deterioration on deodorizing efficiency
・High versatility as it has an ability of processing most of organic substance
・Less fluctuation of deodorizing efficiency in spite of the fluctuation of odor origin
・Easy maintenance and no parts replacement needed
Disadvantage:
・Higher operation cost because of high heating temperature
・Due to high heating temperature, amount of nitrogen oxide emission is little higher than other systems
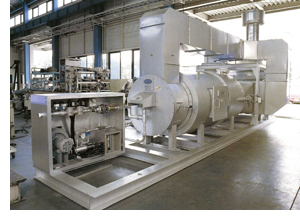
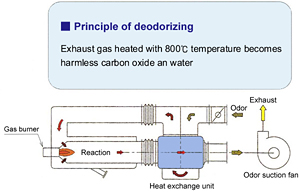
【applicable industry】
・Paint drying equipment
・Paint booth
・Gravure printing machine
・Off-set printing machine
・Food processing
・Sludge dryer
・Human waste disposal unit
・Food waste disposal unit
・Exhaust gas from various heat processing installation
Deodorizing equipment with catalytic combustion system
Odor is heated with 200 to 300℃and put through the catalyst (refer to the drawing on the right). The odor element oxidized, decomposed and become harmless(chemical reaction is the same as direct combustion system). Cost of fuel for heating can be largely saved and costly refractory materials won’t be needed. Its durability is excellent and is the best system from the safety aspect as well.
By installing exhaust heat recovery unit, the operation cost for this deodorizing system can also be saved.
The catalyst is made of porous and large surface area materials such as alumina cordierite and metal as well as active materials like platinum and palladium for supported materials.
Advantage:
・High deodorizing effect and reliable
・Lower operation cost because of low combustion temperature operation
・Catalytic reaction heat makes it lower operational cost
・Lower emission of NOx
Disadvantage:
・Pretreatment may be needed due to impregnation of toxic material(makes catalyst deteriorated)
・Exhaust component makes the maintenance cost higher because catalyst needs to be cleaned to avoid the deterioration of it.
・Higher cost of catalyst makes the initial cost higher
・Heat resistant countermeasure is needed for the heat generated by catalytic reaction
※Catalyst poison
(temporally poisoning substance)
Tar, Cl, Br, F, K, Na
(permanent poisoning substance)
S, P, Si, As, Pb, Sn, Sb, Zn, Hg
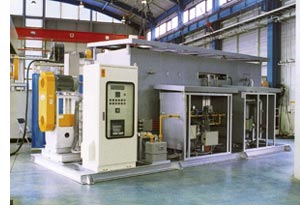

【applicable industry】
・Paint drying equipment
・Paint booth
・Organic chemical industry
・Petrochemical industry
・Gravure printing machine
・Off-set printing machine
・Food processing
・Sludge dryer
・Human waste disposal unit
・Food waste disposal unit
・Exhaust gas from various heat processing installation
Deodorizing equipment with heat reserve combustion system
Exhaust with odor is combustion with 800 to 900℃, the odor in exhaust is oxidized and decomposed with high temperature.
The exhaust becomes harmless as a result.
(the system is same as direct combustion system) The exhaust is passed through the heat reservoir with high heat exchange efficiency. Heat carried by the exhaust is absorbed by the heat reservoir. The heat increases temperature of the exhaust and deodorized in the combustion chamber. This higher heat exchange efficiency system than the direct combustion system makes it possible to decrease the consumption of the fuel a lot lower than the direct system.
The heat chamber unlike catalyst or activated coal, does not age that leads to less maintenance cost such as parts replacement. Nicotine and tar that may clog the heat chamber needs to be watched carefully. Warm-up operation takes longer than other systems does due to the heat chamber’s heat absorption period but, it is suited to longer operation time.
Advantage:
・Higher heat exchange efficiency and lower fuel consumption
・Able to operate under high air flow
・Heat chamber’s life is semi-permanent
・Easy to maintenance
・Lower emission of NOx
Disadvantage:
・Larger equipment, larger installation space needed
・Heavier equipment
・Longer warm-up period
・Tar and nicotine is likely to adhere to the equipment damper
・At the time of switching the damper, sudden air flow and pressure may occur
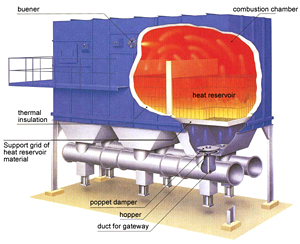
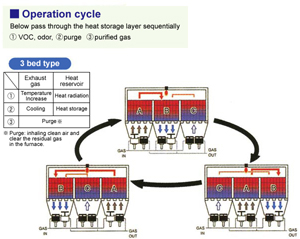
【applicable industry】
・Paint drying equipment
・Paint booth
・Gravure printing machine
・Off-set printing machine
・Food processing
・Sludge dryer
・Human waste disposal unit
・Food waste disposal unit
・Exhaust gas from various heat processing installation
Comparison chart for deodorizing equipment
Direct combustion system | Catalytic combustion system | Heat reserve combustion system | |
---|---|---|---|
Initial cost | Low | Medium | High |
Operation cost | High | Medium | Low |
Deodorizing efficiency | 95%~ | 99%~ | 98%~ |
Heat efficiency | 50~70% | 50~60% | 90~96% |
CO2/NOx rate | High | Medium | Low |
Temperature controlled | 700~800℃ | 250~300℃ | 800~900℃ |
Operational system | High concentrated solvent |
Medium concentrated solvent |
Medium concentrated solvent |
Maintenance cost | Small | Large | Medium |
Feature | Compact and light weight |
Low temperature processing |
Low operational cost |