

Self-Recuperative Burner
ECONEXT-Prime (ENX-P) burner is a latest industrial gas burner of "ECONEXT" series.
The ENX-P burner has high energy saving performance by heat exchanger,
and the design based on high temperature air combustion technology can significantly reduce NOx emission caused by the thermal NOx mechanism.

Benefit
- - Compact shape by integrating burner and heat exchanger
- - Achieve fuel saving of up to 30%
- - NOx emission reduction by high temperature air combustion technology
- - Designed for high durability
- - Lightweight and simple structure for ease of maintenance
- - Highly reliable ignition by using swirling flow inside a pilot burner
- - Uniform temperature distribution
High temperature air combustion technology
ENX-P adopts two-stage combustion technology composed of a pilot and a main burners.
The pilot burner works for the mixing of preheat air and burned gas to produce low-oxigen and high-temperature oxidizer (diluted high temperature air) for main combustion, and also for the ignition of the main combustion.
The high temperature air combustion is implemented in the main burner.
The technology enables low NOx combustion by keeping the flame temperature below 1,800K.
Thus, ENX-P enables the high temperature air combustion by a burner system.
ENX-P allows the high temperature air combustion even using relatively low temperature air below 1,000K.
This is because the pilot burned gas and hot air are mixed.
Figure 1 shows high temperature air combustion conditions.
ENX-P realizes low NOx stable combustion even though the air temperature is lower than 1,000K.

Outstanding energy saving rate
Figure 2 shows energy saving rate (ηe) against tempreture at the inlet of heat exchager (T1) .
Recovering exhaust heat can reduce heat input and fuel consumption.
It is estimated that ENX-P can reduce fuel consumption up to about 30% compared to without exhaust heat recovery.
Furthermore, the reduction of fuel consumption can simultaneously reduce CO2 emissions.
ηe: energy saving rate [%]
P: recovered heat input[kJ/s]
H:burner output [kJ/s]
G1:fuel consumption [kg/s]
G2:fuel rate [kg/s] estimated from the heat which the air has received from the exhaust gas

Uniformization of furnace temperature distribution
Figure 3 shows ordinary combustion (left) and high temperature air combustion (right, ENX-P) .
Combustion generally proceeds rapidly in the vicinity of the burner, where local high temperature zones occur.
Then, the temperature distribution in the furnace becomes higher at the center of the furnace.
On the other hand, since ENX-P burns slowly throughout the furnace based on high temperature air combustion,
the temperature distribution in the furnace becomes uniform.
As the result, miniaturization of the furnace, improvement of the quality of heating object, and reduction of NOx emission become possible.

Comparison with conventional type burner
Figure 4 shows an example of exhaust heat recovery.
The conventional type burner discards the effective heat contained in the exhaust gas.
On the other hand, ENX-P can recover a part of the effective heat to decrease the exhaust gas temperature from 900 ℃ to 500 ℃.
The recovered heat is transferred to the air through heat exchanger to make preheated air.
This means that ENX-P is able to reduce fuel consumption.

Heat exchanger effectiveness
Figure 5 shows the heat exchanger effectiveness (ε) against the temperature at the inlet of heat exchanger (T1) .
The effectiveness becomes 60% - 70%.
ε:heat exchanger effectiveness
T1:temperature at the inlet of heat exchanger
T2:preheated air temperature
T4:atmosphere temperature (supplied air temperature)

Reduction of NOx emission
Figure 6 shows NOx emission, preheated air temperature (T2) , and exhaust gas temperature (T3) against the temperature at the inlet of heat exchanger (T1) .
NOx formation is strongly dependent on temperature, in particular exponentially over 1,800K.
ENX-P can significantly reduce the NOx emission based on the preheated air combustion technology which is able to make uniform temperature distribution below 1,800K.

Burner performance(LHV) min. / max. capacity | 15kW / 120kW | |
---|---|---|
Fuel | Natural gas | |
Supply pressure | Fuel | 15kPa |
Combustion air | 10kPa | |
Heatresistant temperature | 900°C | |
Burner control | on / off, position, PID | |
Flame detector | UV phototube | |
Weight | 70kg | |
Typical application | Aluminum melting furnace | |
Crucible furnace | ||
Heat treatment furnace | ||
Ladle preheating | ||
Drying furnace |

When putting solid metal into the furnace with fused metal inside, the temperature of the furnace gets reduced and needs to be heated again.
This furnace saves energy cost by increasing the temperature of preheat air for the burner with the exhaust heat and lower the calorie for heating.
Equipment | Crucible type fusion furnace |
---|---|
External size | φ1,980xH1,550 (furnace) φ1,050xH600 (crucible diameter) |
Controlled temperature | 480℃ |
Heat source | 13A |
Burner | ENX-240(240kW) |
Material | External: Painted steel plate |
Others | 2,000kg/hr |

▲Dolly type annealing furnace
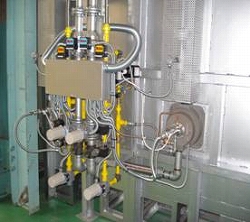
▲ECONEXT
Transport system that puts parts in and out furnace is using the truck of self-propelled type.
And we can achieve large fuel saving by using ECO burner.
Equipment | Dolly type annealing furnace(10t type) |
---|---|
Transport type | Self truck |
External size | W3,500xH3,000xD6,000 |
Processing capacity | 10t/charge (15t/charge :including dolly) |
Temperature | MAX1,000℃ |
Heat source | LNG |
Burner type | ENX-120 120kW type×10 unit |